Durchschaubarer
Expertenrunde ‘Inline-CT: Mythos oder Realität?’ – Teil 2/2
Auf der Control 2018 haben Experten von Aptiv, Fraunhofer IIS, Volume Graphics, Werth und Yxlon über die Möglichkeiten und Anforderungen der Inline-CT diskutiert. Im zweiten Teil der Expertenrunde geht es dieses Mal um Usability und Predictive Maintenance Ansätze.
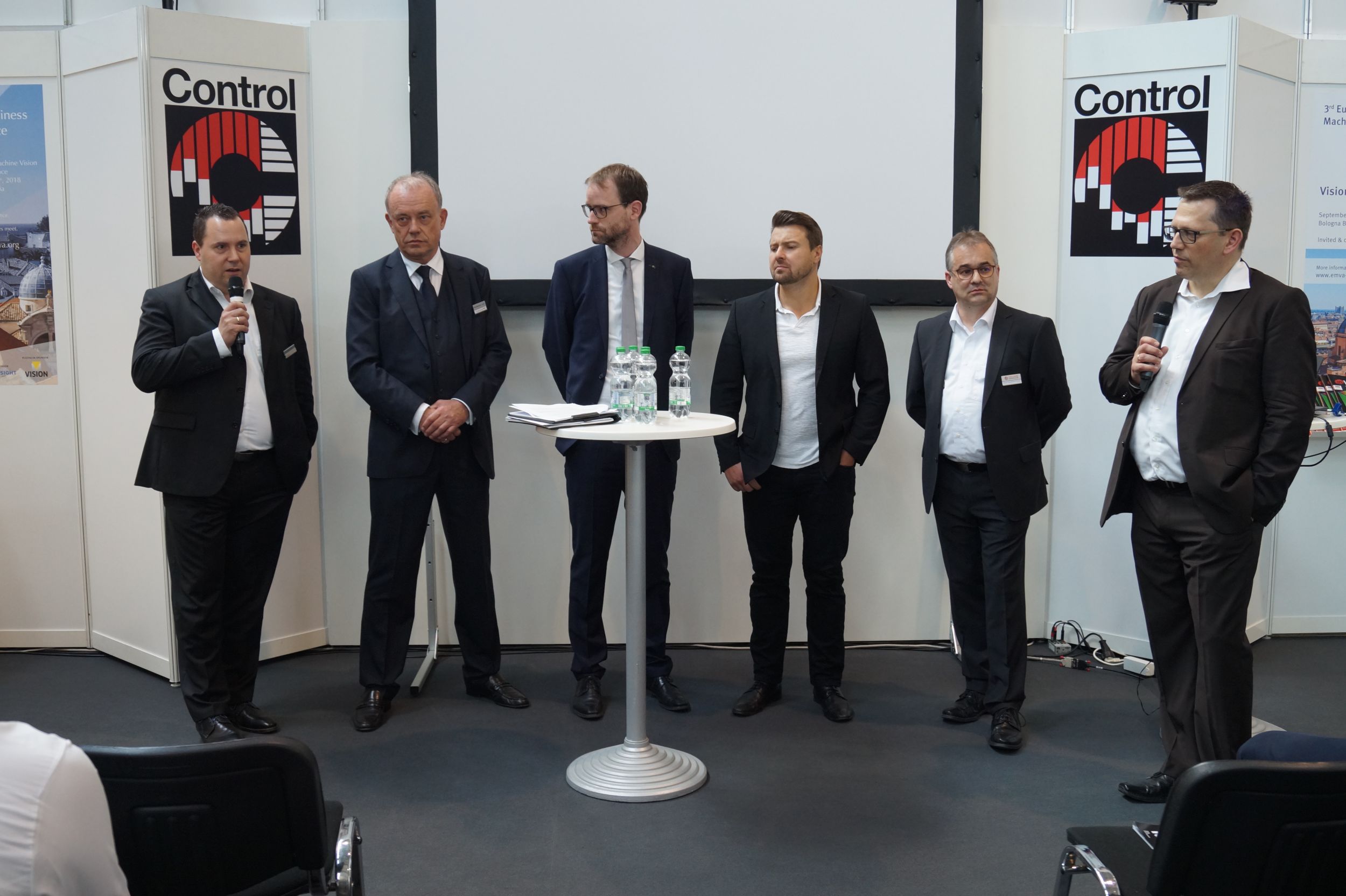
Die Teilnehmer der Inline-CT Expertenrunde (v.l.n.r.): Lars Siefke (Yxlon International), Dr. Ralf Christoph, (Werth Messtechnik), Christian Kretzer (Fraunhofer IIS), Patrick Nikolajko (Aptiv), Dr. Sven Gondrom-Linke (Volume Graphics) und Dr.-Ing. Peter Ebert., (Bild: TeDo Verlag GmbH)
Welche Wünsche haben Sie an die Software?
Patrick Nikolajko (Aptiv): Bisher haben wir als Endergebnis einen PDF-Report bekommen. Das war aber für uns nicht mehr ausreichend. Wir wollen eine Entscheidung haben, ob ein Fehler vorliegt oder nicht. Dazu brauche ich ein dynamisches 3D-Bauteil, das ich drehen kann, um den Fehler zu erkennen. Wenn ich z.B. einen Stecker mit 40 Kammern und einen Kernbruch habe, bekam ich bisher nur ein 2D-Bild. Welche Kammer aber von dem Fehler betroffen ist, wusste niemand. Unser Wunsch war es ein Tool zu bekommen, bei dem ich Fehler visualisieren kann, bzw. von Fehler zu Fehler springe, um zu entscheiden, diesen Fehler akzeptiere ich und diesen nicht. Dieses Tool haben wir jetzt mit dem Inline Approver von Volume Graphics.
Was macht der Inline Approver genau?
Dr. Sven Gondrom-Linke (Volume Graphics): Das ist ein Software-Tool, mit dem Sie die Möglichkeit haben, Daten manuell nachzubewerten. Die meisten Inline-Anlagen sind Vollautomaten, d.h. sie treffen automatisiert Gut-/Schlecht-Entscheidungen. Wenn Sie ihren Produktionsprozess verstehen und notfalls auch gegensteuern wollen, bevor Sie Ausschuss produzieren, brauchen Sie aber die Möglichkeit, die Ergebnisse auch manuell anzuschauen, d.h. die Anlage ggf. zu überstimmen. In manchen Branchen ist eine manuelle Nachprüfung sogar vorgeschrieben.
Christian Kretzer (Fraunhofer IIS): Die Hardware ist vorhanden und hat ihre physikalischen Grenzen. Das entscheidende Kriterium, das man neu einbringen kann, ist das Element Software, bei dem noch sehr viel Potenzial vorhanden ist. Zum einen bei Auswertealgorithmen, die selbstlernend sind und automatisch entscheiden, was ein Pseudo- oder ein echter Fehler ist. Dies mit deutlich geringeren Rechenzeiten, z.B. für eine Datenvisualisierung, damit der Anwender die komplexen 3D-Volumen erfassen kann und so schnellere Entscheidungen möglich sind.
Dr. Ralf Christoph (Werth Messtechnik): Die Software ist ein Schwerpunkt der derzeitigen Entwicklungen, um z.B. Fehler im Werkstückvolumen visualisieren zu können. Zudem müssen die Maße korrekt und rückführbar ausgegeben werden, was bei einem konventionellen Koordinatenmessgerät selbstverständlich ist. Auch muss das Gerät leicht bedienbar sein. Verschieden qualifizierte Personen arbeiten an einem Gerät.
Lars Siefke (Yxlon): Die Usability ist natürlich entscheidend. Es ist wichtig, dass der Kunde selbst Prüfprogramme erstellen und auch verändern kann. Wo man auch derzeit daran arbeitet, sind die Rekonstruktionsalgorithmen. Wie kann ich mit weniger Projektionen die gleiche Bildqualität erzeugen? Damit ergäbe sich eine deutliche Reduktion der Scanzeit und damit eine Erhöhung des Anlagendurchsatzes.

„Wir wollen, dass die Software selbstständig erkennt, welches Bauteil ich habe und aus was für einer Kavität das Teil kommt, also eine direkte Fehlerzuordnung.“ Patrick Nikolajko, Aptiv (Bild: TeDo Verlag GmbH)
Kann hier evtl. Deep Learning helfen, um bessere Ergebnisse zu bekommen?
Gondrom-Linke: Natürlich ist Deep Learning ein Thema, aber auch die klassischen, analytischen Ansätze sind noch nicht ausgereizt. Beim Deep Learning muss man aber aufpassen, nicht dem Hype zu erliegen, denn alles, was Sie nicht trainieren, finden die Algorithmen später auch nicht. Alles was Sie dagegen an Information reinstecken, werden sie finden, selbst wenn es nicht da ist..
Kretzer: Sie brauchen selbstlernende Algorithmen, die im Hintergrund arbeiten, um manuelle Nachentscheidungen überflüssig zu machen. Das geht soweit, dass Sie sogar die Parameterfindung komplett automatisieren. Der Anwender will seine Parameter selber festlegen können. Wenn eine Bauteilabweichung kommt, möchte er nicht an einen externen Dienstleister Geld zahlen, damit er ein neues Prüfprogramm bekommt, sondern es sofort selber machen. Ziel ist, dass der Anwender ein Bauteil in das CT-Gerät legt und alle Parameter, die er benötigt, automatisch von Algorithmen bestimmt werden.
Nikolajko: Wir wollen schneller werden, d.h. nicht nur ein Bauteil scannen, sondern dass die Software auch selbstständig erkennt, welches Bauteil ich habe und aus was für einer Kavität das Teil kommt. Also eine direkte Fehlerzuordnung, die dann intern evtl. noch mit unserem SAP System verknüpft wird, damit wir notfalls sofort die Auslieferung von Schlechtteilen stoppen können.
Aus den Daten kann man mittlerweile also deutlich mehr lesen als IO/NIO?
Siefke: Das ist richtig. Man muss nicht nur 100% gut oder schlecht entscheiden, man kann auch gewisse Warnlevels definieren und sagen: Hier läuft irgendetwas verkehrt. Um diese Daten aber nutzen zu können, muss es Schnittstellen zu den Kundensystemen geben. Wenn man nur jedes 100. Teil prüft, muss man bei SAP die Auslesung stoppen können, denn dann wurde u.U. ein bisschen zu spät geprüft. Letztendlich geht es darum, deutlich schneller als bisher, brauchbare Ergebnisse zu bekommen.
Frage aus dem Publikum: Michael Salamon (Fraunhofer IIS): Wie sieht es mit der Anfälligkeit eines Inline-Gerätes mit offenen Röntgenquellen aus?
Gondrom-Linke: In meiner früheren Tätigkeit bei einem Hardwarehersteller haben wir bereits 2009 bei Infineon ein Elektronik-Prüfsystem mit CT und einer offenen Röhre eingerichtet. Das System läuft bis heute 24/7 und Infineon hat fünf Systeme nachgekauft.
Christoph: Wir haben letztes Jahr ein Produkt mit einer speziellen offenen Röhre vorgestellt, bei dem wir auf einen 12-monatigen Wartungszyklus kommen.
Gondrom-Linke: Worauf die Frage aber letztendlich hinausläuft: Kann ich irgendwie erkennen, dass eine meiner Hardwarekomponenten wegdriftet, d.h. evtl. demnächst kaputt geht oder eine Wartung braucht? Gerade ein Inline-Gerät ist anhand der Vielzahl ähnlicher Daten, die es erzeugt, prädestiniert , die Scan-Qualität zu überwachen. Verschlechtert sich die Qualität des Scans, kann man präventiv tätig werden.
Siefke: Gerade beim Thema ‚Inline‘ spielt Service eine herausragende Rolle und es ist überaus wichtig, dass man schnell vor Ort ist. Daher bieten wir auch verschiedene Service-Konzepte an. Ein Museum kann evtl. zwei Wochen auf ein CT-System verzichten, während es bei einer Gießerei anders aussieht.

„Ziel ist, dass der Anwender ein Bauteil in die CT legt und alle Parameter, die er benötigt, automatisch von Algorithmen bestimmt werden.“ Christian Kretzer, Fraunhofer IIS (Bild: TeDo Verlag GmbH
Gibt es bereits Predictive Maintenance Konzepte bei der CT?
Christoph: Bei Komponenten, die verschleißen, gibt es bereits eine Art Ampel, auf der man den aktuellen Zustand seiner Anlage sehen kann. Das gab es beispielsweise vor zehn Jahren noch nicht.
Salamon: Bei offenen Röhren gibt es aber verschiedene Komponenten, die alle für sich Probleme bereiten könnten. Es ist ein Unterschied, ob ich eine Röhre nehme, die in der Gepäckdurchleuchtung eingesetzt wird und einfach ihre Stundenanzahl abbrennt oder eine offene Röhre, die alle 300 bis 400 Stunden komplett saniert werden muss.
Siefke: Wir wählen natürlich eine Röhre nicht nach dem Kriterium aus, ob sie offen oder geschlossen ist, sondern schauen immer auf die Anwendung. Offene Quellen bieten für viele Anwendungen herausragende Eigenschaften, die den höheren Wartungsbedarf in den Hintergrund drängen. Mit unseren neuen Entwicklungen können wir allerdings auch zeigen, dass der Wartungsbedarf für offene Quellen reduziert werden kann und damit dem Einsatz in Inline-Anwendungen nichts im Wege steht.
Christoph: Unsere Geräte messen auch bei den großen Automobilzulieferern Einspritzdüsen mit unserer Mikrotaster-Technologie und CT-Geräten. Dort haben wir z.B. seit Jahren 190kV-Transmissionsröhren im Vierschichtbetrieb im Einsatz, also sieben Tage die Woche 24/7, und das funktioniert. Man kann nicht jede Röhre dafür nehmen, aber es gibt durchaus offene Röhren, mit denen das klappt.
Ist die CT ein ausgereiztes Verfahren oder gibt es auch neue Einsatzgebiete?
Siefke: Wir sind noch lange nicht am Ende. Ein völlig neues Feld ist z.B. die Additive Fertigung. Dort sind wir zwar noch am Anfang was die Produktion angeht, aber beim Prüfen sind wir schon sehr dicht dran.
Christoph: Ich kenne das bereits aus der Bildverarbeitung. Nach 20 Jahren denkt man, es fällt einem nichts Neues mehr ein, aber dem ist nicht so. So haben wir z.B. heute bei der Prüfung von Einspritzdüsen Maße, die auf vier Mikrometer toleriert sind. Da „Messmittelfähigkeit“ nach den üblichen Automobilnormen gefordert ist, müssen wir Messunsicherheiten unter einem halben Mikrometer realisieren. Wenn ich das vor zehn Jahren jemandem erzählt hätte, als wir CT für Koordinatenmesstechnik eingeführt haben, hätte dies wohl keiner für möglich gehalten.
Kretzer: Es gibt bereits erste Entwicklungen in Richtung der In-Process-CT. Also nicht nur ein Bauteil zu prüfen, wenn es bereits fertig ist, sondern sich den Aufbauprozess des Bauteils direkt im Prozess anzuschauen. Eine weitere Anwendung wäre es, mittels CT zu verfolgen, wie ein Fahrzeug gegen eine Wand fährt und sich die Bauteile dabei verformen. Das ist allerdings noch Zukunftsmusik.
Nikolajko: Die Konstrukteure wollen bei uns mittlerweile ihr Produkt lieber mit einem CT-Gerät gemessen haben. Ich kann mich noch an die Anfänge der CT bei uns erinnern. Zuerst war man sehr skeptisch und hat gesagt, miss das Teil nicht mit CT, sondern konventionell. Heute sagen alle, miss mein Bauteil lieber mit CT und nicht konventionell, da das CT-Gerät genauer ist. Ich kann deutlich mehr sehen und bin durchschaubarer, im wahrsten Sinne des Wortes. Unsere Konstrukteure schauen sich auch den Datensatz sehr genau an, wie und wo wir was gemessen haben. Das ist nicht nur bei uns im Labor so, sondern mittlerweile auch bei den Ingenieuren außerhalb des Labors. Auch die wollen sicher sein, das ihr Bauteil OK ist und zum CAD passt.
Gondrom-Linke: Ich mache seit 22 Jahren CT und es kommt jeden Tag etwas Neues. Ich habe nicht die geringste Befürchtung, dass ich mich bis zur Rente an einem einzigen Tag langweilen werde.
Wie lange schätzen Sie dauert es, bis die Inline-CT flächendeckend im Einsatz ist?
Gondrom-Linke: BMW geht davon aus, dass sie in zehn Jahren bei den Neuanschaffungen mindestens die Hälfte heutiger 2D-Anlagen durch 3D-Systeme ersetzt haben werden. Das sagt eigentlich alles.

„BMW geht davon aus, dass sie in zehn Jahren bei den Neuanschaffungen mindestens die Hälfte heutiger 2D-Anlagen in 3D haben werden.“ Dr. Sven Gondrom-Linke, Volume Graphics (Bild: TeDo Verlag GmbH)
Nikolajko: Ich hoffe, dass wir in fünf Jahren an jedem Standort ein CT-Gerät haben und inline prüfen.
Kretzer: Es wird auch in Zukunft Anwendungen geben, bei denen es mehr Sinn macht, eine Radioskopie-Stufe in 2D zu machen und nicht eine Messung mit Inline-CT. Flächendeckend wird sich die Inline-CT aber die nächsten zehn Jahre deutlich verbreiten.
Christoph: Ich würde das Ganze nicht nur aus der Sicht der Röntgensensorik betrachten. Im Verhältnis zu den verfügbaren Technologien für das dimensionelle Messen ist CT bloß eine Nische, wenn auch mit zunehmender Bedeutung. Für einige Anwendungen, wie z. B. die additive Fertigung, ist die CT sehr gut geeignet. Das sind zwei Verfahren, die wie füreinander gemacht sind. Allerdings dauert es Jahrzehnte, bis sich eine solche neue Technologie in der Breite durchsetzt. Das hängt letztlich auch von den Kosten ab.
Siefke: Wenn es bei der gut/schlecht Entscheidung bleibt, dann wird Inline-CT noch einen langen Weg haben. Wenn aber die Kunden bereit sind, darüber hinaus zu schauen und die statistischen Daten eines CT-Gerätes auch nutzen, für die Produktionsoptimierung einzusetzen, dann wird die Inline-CT in den nächsten vier bis sechs Jahren die Mehrheit der Inline-Röntgen-Systeme stellen.
Teilnehmer
Patrick Nikolajko,
Global CT & Metrology Manager,
Aptiv (ehemals Delphi)
Christian Kretzer,
Gruppenleiter Applikationen,
Fraunhofer IIS
Dr. Sven Gondrom-Linke,
Teamleader Technical Consulting, Volume Graphics
Dr. Ralf Christoph,
Geschäftsführer,
Werth Messtechnik
Lars Siefke,
Senior Sales Manager,
Yxlon International